Optimal freedom of form
Respond Quickly on changing demand
You can find items that are 3D printed everywhere. Jansen Medicars also incorporates 3D printed parts into their furniture.
These products are not only supplied to all hospitals in the Netherlands, but find their way all over the world. And those products – in short: solutions to make medical equipment mobile– use parts printed by Parts On Demand.
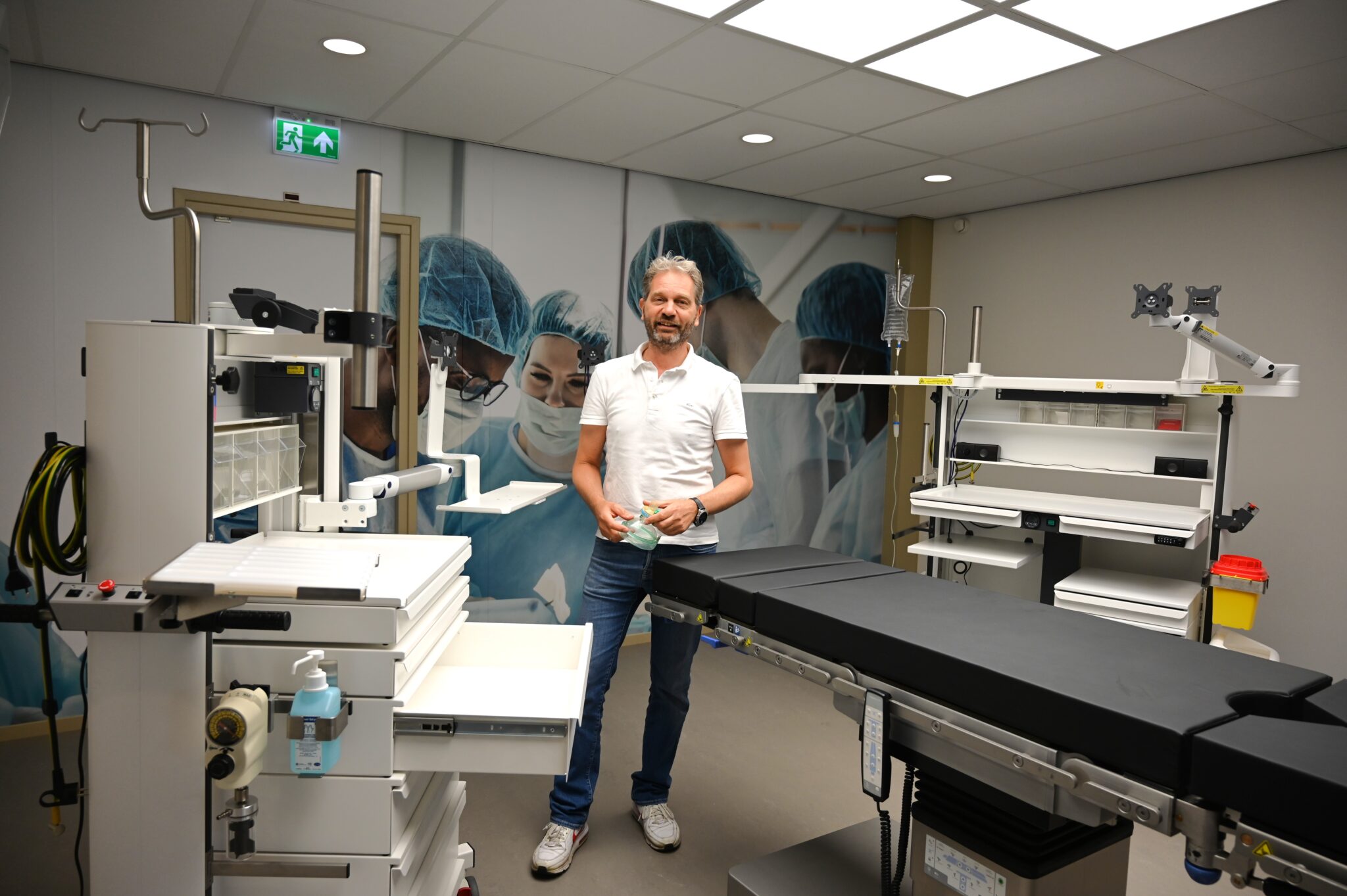
Inhoudsopgave
First let’s talk about those products. You will recognize them most quickly as trolleys on which medical equipment can be moved across hospital wards. Think of ventilators, but also endoscopy, ECG equipment and equipment for data management. But besides those trolleys, which sounds somewhat disrespectful if you have had a look behind the scenes at this company, Jansen Medicars makes much more. Consider wall and ceiling systems for operating rooms, equipment trolleys for intensive care, carrying systems for cardiology applications and mobile battery power supplies for transport incubators.

From schools to hospitals
Ronald Haandrikman nam samen met zijn vrouw Linda het stokje over van de vader van Linda, die het bedrijf in 1971 begon. “Mijn schoonvader was vertegenwoordiger in schoolboeken en maakte op een gegeven moment een karretje voor die boeken. Hij was nogal creatief en altijd bezig om iets slim te bedenken. Hij ontwikkelde bepaalde leermiddelen zoals een rekenlineaal voor klassikaal gebruik, maar ook podiumelementen voor de voorstellingen in de scholen. Toen SchoolTV zijn intrede deed, had hij daar al snel een karretje voor ontwikkeld, wat doorgroeide naar verrijdbare afsluitbare kasten omdat de verzekering dat vanwege de diefstalgevoeligheid eiste.”
One thing led to another. And when father Jansen also had many hospitals as customers in the 1980s, he started developing specific furniture for medical applications. “That medical application placed more and different demands on the carts. For example, they had to be provided with more sockets than the school carts. But hygiene and the possibility of using them for different equipment also required a specific design. And then you can also immediately adapt the material and color to medical applications.”
Focus
Ronald has been working at Jansen Medicars since 2003 and in 2006 he and his wife took over the company completely. “That was the moment we stopped offering products for schools and started focusing entirely on medical applications. We now had a good idea of the medical application and that involves completely different aspects. We have carefully considered the application and structure of the trolleys and developed a modular concept with a number of standardized basic trolleys. Such a basic trolley is a base with one or two uprights, on which the desired number of shelves, arms, power supplies, bottle holders and a large number of other accessories can be selected as desired. With these ingredients, a trolley can be built to customer specifications. We have almost all individual components of a trolley in stock here and the system can be quickly assembled. This means that an ordered trolley can be delivered quickly, custom-made from stock, as it were,” he laughs.
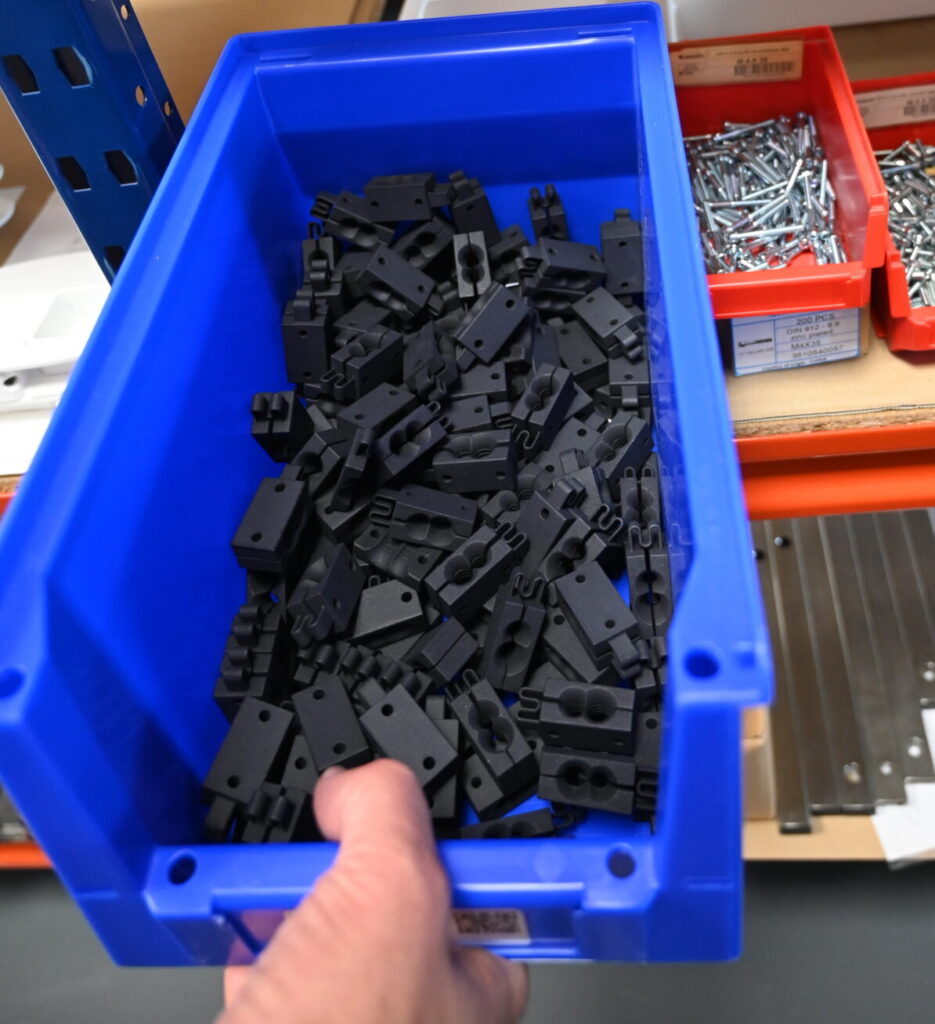
Worldwide
The trolleys find their way all over the world. The rest of the world is also served through a network of international resellers with a focus on Europe, but often through resellers. “We also make products for equipment suppliers. They want to be able to supply a trolley with their own product and this also involves somewhat larger quantities.” There are now quite a few suppliers of such equipment who immediately include the trolley when offering it to hospitals. “During the corona period, we received a request for a trolley to place a ventilator on. And if we could make 500 right away, delivery time would preferably be yesterday.” He laughs when he thinks back to the hustle and bustle of that time. “We have developed a completely new trolley for this customer. The question came on Monday, on Tuesday we had a design, on Wednesday we received the order and a week and a half later the first fifty pieces had already been delivered. These are moments when your suppliers are important. You really need them to realize something like this. For this assignment, people worked until midnight to help us make this happen.”
The trolleys are designed to be durable and some have been in use for no less than forty years. “We use high-quality materials such as stainless steel, aluminum and steel. We don’t even need a service organization, because our products are not prone to failure.” The designs of the trolleys are made in-house, production is based on quantities and costs and part is outsourced. “For very special requests or urgent orders, we have a production department with all the machines to produce ourselves.”
Production techniques
When it comes to production techniques, Haandrikman is keenly aware of developments. The company has now also firmly embraced 3D printing technology. “We used 3D printing techniques for prototyping and proof-of-concept, but the quality was often insufficient. When the technology of 3D printing continued to improve, we wanted to know more about it and three of us visited Parts On Demand. The options were explained in detail there. It is very nice that you can upload a 3D model directly to the website and order one-on-one. And 3D printing of course offers enormous freedom of form. Because printing techniques have improved significantly in recent years, we also have Parts On Demand print parts that we use in the assembly of the trolleys. For example, the strain reliefs for the power cords are no longer CNC-milled, but 3D printed. This allowed us to improve the product and make it cheaper. We also have other parts printed, such as pole clamps and holders for remote controls.”
“At the start of the collaboration with Parts On Demand, we first tried something to see what the quality was and how the process works. We were pleasantly surprised by the quality and gradually we started thinking more about the use of 3D printing in the design process. We receive many custom requests for single pieces, where a good solution can often be achieved with a 3D print. We create the design in Solid Works and then you immediately have the correct file for the order.”
Cooperation
Haandrikman is positive about the collaboration with Parts On Demand. “If you have technical questions, there is always someone available to help us with ideas. And we notice that they also check our drawings for printability and, if in doubt, we receive good feedback about, for example, the print direction or wall thicknesses. Everything runs fine, the people are helpful and friendly. And it’s just nice if you have an answer to your question within the foreseeable future. To be fair, that’s why we’re still customers. For bulk quantities we order from Parts On Demand and in some cases we print something in-house. But it just looks nicer if we have it printed there. The technique they use gives a better result. The price, the freedom of design and the delivery time, nothing but advantages!”
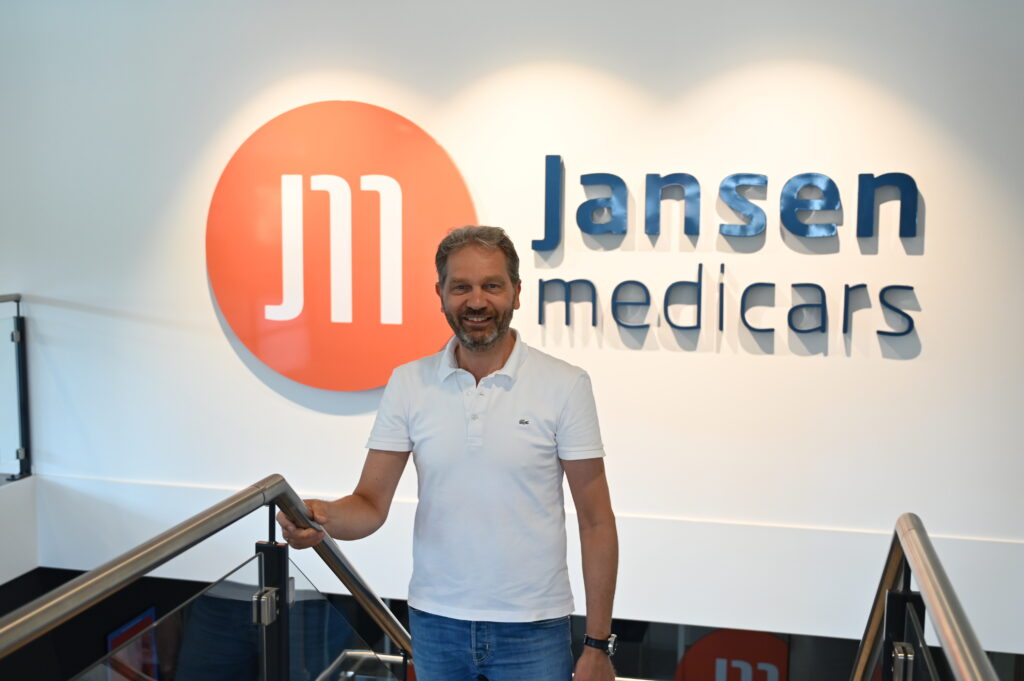
Fifty years of trolleys
Medical trolleys have changed considerably over the last twenty years. “We use many new techniques in production. We use an aluminum extrusion for the sides, which is also a technique that provides great freedom of shape. The equipment that we need to store on it also changes, of course, and more and more equipment and work inventory is being placed on one trolley. For example, one trolley can contain an insullator (a device for blowing in CO2), a light source, a camera, a processor, data storage, flushing and suction pumps and a working stock of consumables.”
A lot of domain knowledge has been acquired over the past twenty years and Haandrikman can also think along with applicants. “We often see different working methods in different places and sometimes that can work to our advantage.” An important topic for these applications is also the stability of the carts. A medical standard defines stability tests that a trolley must meet during movement and use. Haandrikman says that they have developed a calculation model themselves with which they can perform stability simulations. “The trolleys must of course not fall over during all possible use situations.” He shows a high trolley of considerable size on which a huge screen can be mounted. “This one, for example, must remain stable when you drive it. Whether the display is in the high or low position, it must be stable under all conditions. And also think of the trolleys with the swivel arms with monitors attached to them. It is essential that all our products meet safety standards. With this calculation model we also help our customers and start-ups to design smart and efficiently. We like to work closely with all parties and start-ups are also part of that.”
Are you looking for a reliable partner that can scale with you and your business?
Do not hesitate to contact us:
Phone: (+31) (0) 85 4444 200
Email: info@partsondemand.eu