Parts on Demand is one of the five largest buyers of EOS powders for SLS printing with a smaller carbon footprint or even climate neutral.
“They are one of the frontrunners,” says Björn Hannappel, Head of Sustainability at EOS. “With the associated certificates, Parts on Demand can precisely demonstrate the CO2 footprint of printed products. “
Neil, our Geek in Chief, expects that this will be required in the manufacturing industry in five years. “End customers must do an LCA; we are part of the chain.”
We don’t only look for the solution for more sustainable 3D printing in the material…
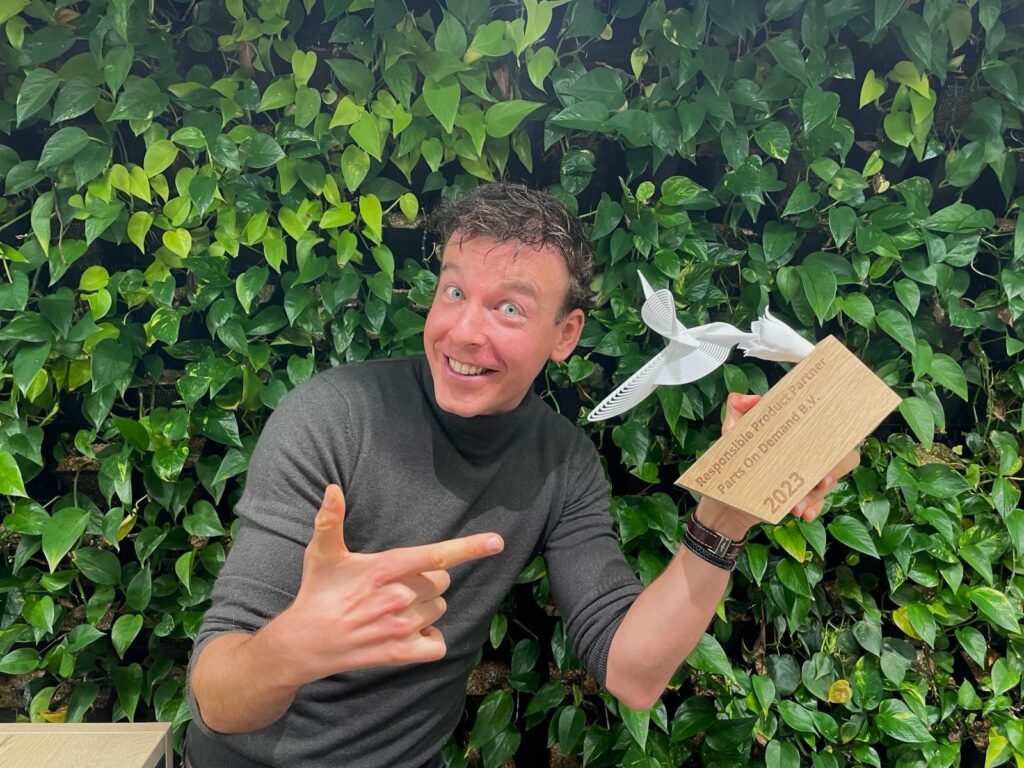
Sustainability is high on the agenda at EOS. Eighteen months ago, the 3D printer manufacturer launched two polymers for SLS printers with a smaller ecological footprint. The first is Bio-based climate neutral PA11 is CO2 neutral thanks to a renewable raw material and compensation by EOS. The second material is Carbon Reduced PA12. This is a polymer based on fossil raw materials, but with a significantly smaller CO2 footprint than the standard PA12 powder, thanks to the use of renewable energy in production.
Parts on Demand recently received the Responsible Product Partner Award from EOS. “We want to support frontrunners who have jumped on these responsible materials; appreciate their initiative and inspire other customers,” says Björn Hannappel about the award.
Certified materials
Fraunhofer EMI has created an LCA for both materials. The carbon emission calculation has been checked by TÜV Süd. The figures are audited externally every year. Customers such as Parts on Demand receive a certificate with which they can demonstrate the CO2 footprint of their customers. Björn Hannappel notices that customers find transparency about the CO2 footprint particularly important.
Standard printing material
So far, it has been the smaller companies that have jumped on this bandwagon and are fully printing with these new materials. That did not surprise Björn Hanappel. “Smaller companies are more agile; owners want to have a positive impact and respond faster. Big companies are like big ships, they need more time to change course. These conversations are still ongoing. But if the course changes, the impact is enormous. So we ultimately count on all our customers to support the transition to Responsible Manufacturing”
At Parts on Demand we have consciously chosen both the climate-neutral PA11 and the low-carbon PA12 with a smaller CO2 footprint;
Whether customers ask for it or not, basically, they get it. The materials fit exactly into our philosophy, says Neil. “With the new materials, customers don’t have to compromise on quality; They get the better value for the environment. This is in line with our philosophy of producing on-demand and locally to have the smallest possible impact on the environment.”
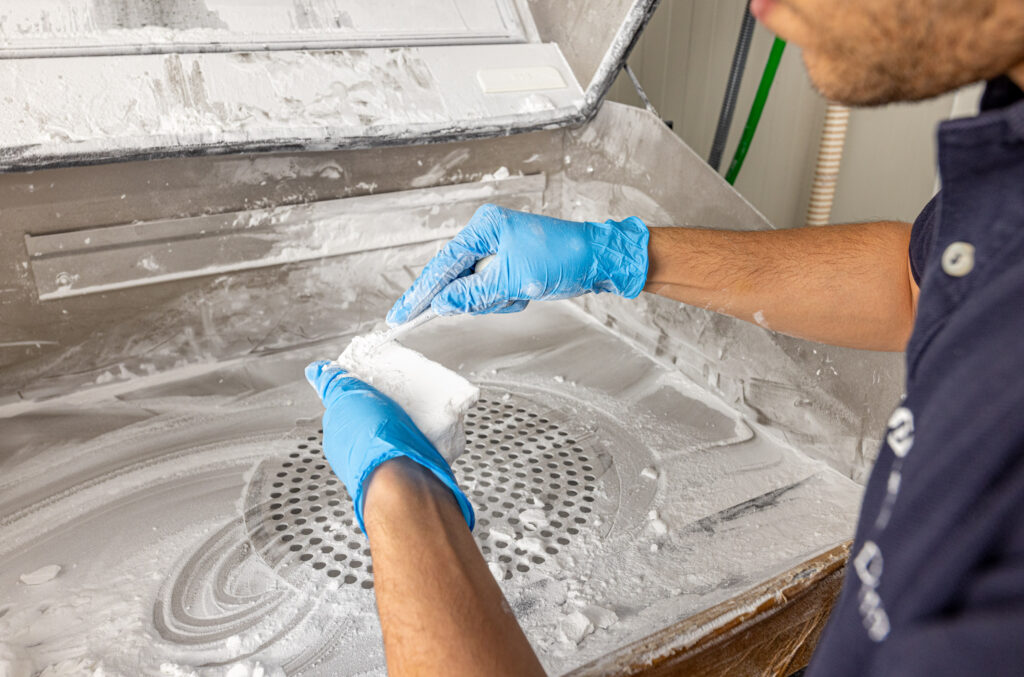
Impact of higher yields
Powders are only part of the solution to make the AM industry more sustainable. The Parts on Demand team is also aware of this.
Further reducing waste is high on the agenda this year, explains Neil. “That starts with improving efficiency and striving for the highest possible yield in production.” The focus at Parts on Demand is on maximum nesting, so that as many parts as possible are printed in one batch and end up in the waste as little as possible in powder. Neil van Es still thinks this is one of the strengths of the SLS printing process. The technology may be slower than other powder-based AM processes, but the yield is higher.
For example, Parts on Demand tries to compensate for the slightly higher purchase price of the more sustainable materials – EOS is responsible for part of the costs. In daily practice, this means combining orders. Isn’t that contradictory to on-demand production, the trump card of 3D printing?
Neil van Es: “We have influence on this because we have many contracts with customers who know in advance how many parts they will need. By combining these orders with ad hoc orders, we achieve the highest possible yield and short lead times.” In addition, his experience is that few customers who order parts want to have them delivered the same week. “Most of them are already very satisfied with a lead time of two to three weeks. That’s already a big improvement compared to injection moulding.”
Certificate will gain in importance
With the corresponding certificates provided by EOS, our customers can include the smaller CO2 footprint in their CO2 calculations.
Few customers specifically ask for this. Neil thinks this will soon change.
“I expect that in five years’ time, certificates and demonstrations of CO2 reduction will be normal in the manufacturing industry. Our customers have to show their customers an LCA and we are part of their chain. The sooner you build up experience with this, the better the solution you can offer.”
Are you required to do an LCA?
Do you already request an LCA from your supliers?
Would you like to discuss this topic any further?
Do not hesitate to contact our team.
info@partsondemand.eu
+31 85 – 4444 200
